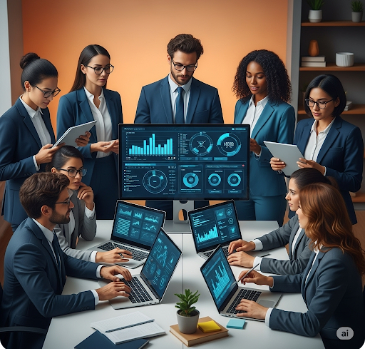
Pessoal, em um cenário empresarial cada vez mais dinâmico e competitivo, a busca por eficiência, inovação e qualidade é essencial para o sucesso das organizações. Ao longo dos anos, diferentes países desenvolveram metodologias que ajudaram empresas a resolver desafios, otimizar processos e impulsionar resultados. São conceitos incríveis e acredito que algum deles pode ajudar você neste momento.
Veja bem: Dos princípios da melhoria contínua do Japão às abordagens analíticas e estruturadas dos Estados Unidos, cada método carrega um legado de experiências e descobertas que moldaram a forma como os negócios enfrentam problemas e encontram soluções.
E é neste artigo que vamos explorar algumas dessas metodologias amplamente utilizadas no setor corporativo, industrial e profissional. Você verá como ferramentas como Kaizen, 5S, Six Sigma, PDCA e Lean Manufacturing podem ser aplicadas para melhorar a produtividade, reduzir desperdícios e criar um ambiente mais eficiente e inovador.
Vamos começar explicando, em resumo, cada conceito. Depois, fique à vontade para explorar profundamente cada um, pois todos é apresentado de forma detalhada e com exemplos. Vejamos primeiramente apresentar a noção destes conceitos:
Métodos Americanos para Resolução de Problemas
No contexto corporativo, diversos métodos foram desenvolvidos por profissionais americanos para endereçar problemas complexos. Um exemplo notável é o Six Sigma, que visa a melhoria contínua através da eliminação de defeitos e variações em processos. Outro método popular é o Lean Management, focado na maximização do valor e na minimização do desperdício, proporcionando uma abordagem altamente eficiente para a resolução de problemas.
Abordagens Japonesas na Resolução de Problemas
Os métodos japoneses, como o Kaizen, promovem uma filosofia de melhoria contínua em todos os níveis da organização. O Kaizen incentiva a participação de todos os colaboradores na identificação de problemas e na proposição de soluções, criando um ambiente de trabalho colaborativo e inovador. Outro conceito importante é o 5S, que visa organizar e padronizar o ambiente de trabalho, facilitando a identificação de problemas e a implementação de soluções rápidas.
Métodos Internacionais Adotados Globalmente
Além das abordagens americanas e japonesas, há uma variedade de métodos que ganharam popularidade em várias partes do mundo. A Resolução de Problemas Através do Design Thinking é uma metodologia que enfatiza a empatia e a criatividade para resolver problemas complexos, principalmente no desenvolvimento de produtos e serviços. Igualmente, o SWOT (análise de forças, fraquezas, oportunidades e ameaças) é utilizado globalmente para realizar diagnósticos e desenvolver estratégias eficazes em ambientes corporativos.
Escolha a metodologia que deseja conhecer:
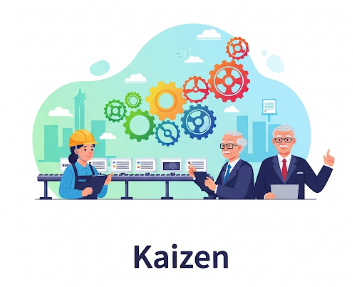
KAIZEN
Uma filosofia que enfatiza o aprimoramento contínuo. Seu foco é realizar pequenas, porém constantes, melhorias em todos os níveis da organização, envolvendo desde os colaboradores da linha de produção até a alta administração. Essa abordagem não só busca a eliminação de desperdícios, mas também promove uma cultura de mudança e inovação diária. Exemplos:
- Desperdício excessivo de materiais e recursos
- Baixa eficiência nos processos produtivos
- Problemas recorrentes na qualidade do produto ou serviço
- Falta de padronização nas operações internas
- Dificuldade na adaptação a mudanças e melhorias contínuas
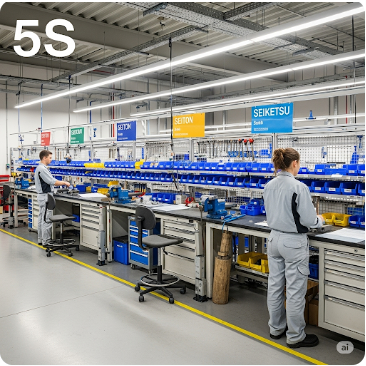
5S
Um método orientado para a organização e padronização do ambiente de trabalho. Os 5S representam: Seiri (organizar ou separar o necessário do desnecessário), Seiton (ordenar), Seiso (limpar), Seiketsu (padronizar) e Shitsuke (disciplinar). Essa técnica contribui para a melhoria da eficiência operacional e da segurança no ambiente laboral. Exemplos:
- Ambientes de trabalho desorganizados e pouco eficientes
- Excesso de materiais desnecessários ocupando espaço
- Dificuldade na localização de ferramentas e documentos
- Falta de limpeza e higiene no local de trabalho
- Ausência de padronização nos processos e fluxo de trabalho
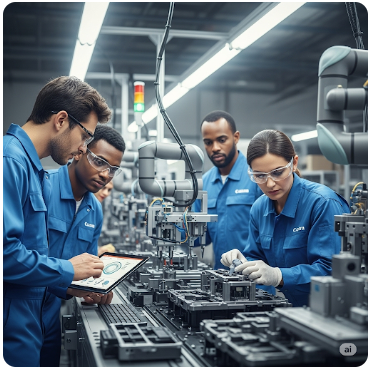
JIDOKA
Também conhecido como “automatização com um toque humano”, esse conceito permite que erros sejam identificados e corrigidos o mais cedo possível durante os processos produtivos, garantindo que a qualidade permaneça consistente. Exemplos:
- Defeitos recorrentes na linha de produção
- Erros humanos não identificados a tempo
- Má qualidade nos produtos acabados
- Interrupções inesperadas no fluxo de trabalho
- Falta de autonomia dos operadores para corrigir problemas
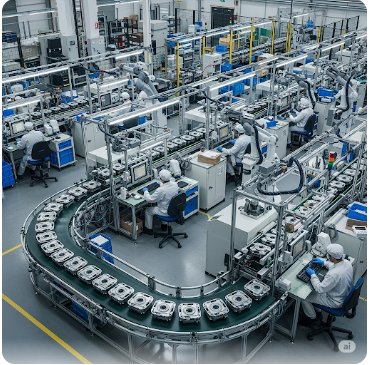
HEIJUNKA
Trata-se do nivelamento da produção, buscando equilibrar a demanda e os processos produtivos. Essa técnica minimiza variações e evita gargalos, proporcionando uma operação mais suave e homogênea. Exemplos:
- Variações bruscas na demanda de produção
- Sobrecarga ou ociosidade dos recursos produtivos
- Gargalos constantes no fluxo de trabalho
- Dificuldade em manter um ritmo de produção estável
- Excesso de estoque ou falta de produtos no momento certo
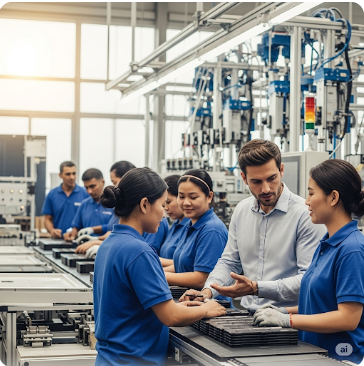
GEMBA
O termo “Gemba” significa “o local real” (como o chão de fábrica) e reforça a importância de os gestores irem até onde os processos acontecem para identificar problemas de forma direta e prática.
- Falta de visibilidade sobre os problemas reais no chão de fábrica
- Baixa comunicação entre gestores e operadores
- Dificuldade em identificar oportunidades de melhoria operacional
- Processos ineficientes sem intervenção direta
- Desconexão entre planejamento estratégico e execução prática
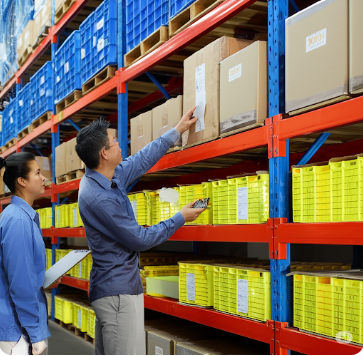
Just in Time (JIT) e Kanban
Esses conceitos fazem parte do Sistema Toyota de Produção (TPS). O JIT busca produzir apenas o necessário, na quantidade certa e no tempo certo, enquanto o Kanban utiliza sinais visuais para gerenciar o fluxo de produção e reposição de materiais. Exemplos:
- Excesso de estoque e altos custos de armazenamento
- Falta de sincronização entre produção e demanda
- Atrasos na entrega de materiais e componentes
- Processos produtivos com desperdício de tempo e recursos
- Dificuldade em visualizar e gerenciar o fluxo de trabalho
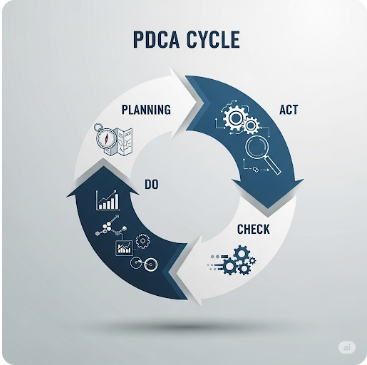
Ciclo PDCA (Plan, Do, Check, Act):
Este é um dos métodos mais tradicionais para a melhoria contínua nos processos. O ciclo PDCA estrutura as ações em quatro etapas — planejar, executar, checar e agir —, proporcionando uma abordagem sistemática para identificar problemas, implementar melhorias, verificar os resultados e instaurar medidas corretivas. Exemplos:
- Processos empresariais com baixa eficiência operacional
- Problemas recorrentes na qualidade de produtos ou serviços
- Dificuldade na implementação de melhorias contínuas
- Tomada de decisão sem base em análises estruturadas
- Falta de padronização e controle nos processos internos
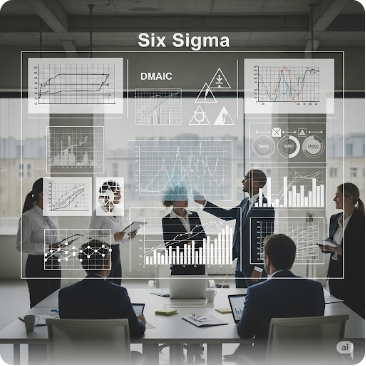
Six Sigma
Embora não tenha sido detalhado nos resultados acima, esse método é amplamente reconhecido no ambiente corporativo americano. O Six Sigma utiliza técnicas estatísticas para eliminar defeitos e reduzir a variabilidade dos processos, contribuindo para a excelência operacional e melhoria da qualidade. Exemplos:
- Alta variabilidade nos processos de produção
- Defeitos frequentes em produtos ou serviços
- Custos elevados devido a desperdícios e ineficiências
- Dificuldade em tomar decisões baseadas em dados concretos
- Processos desestruturados sem padronização e controle de qualidade
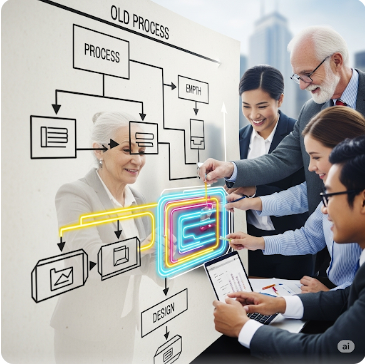
Business Process Reengineering (BPR) e Design Thinking:
O BPR propõe uma reengenharia radical nos processos de negócio para alcançar melhorias significativas, enquanto o Design Thinking foca na resolução de problemas complexos através da empatia, criatividade e prototipagem, incentivando soluções inovadoras em contextos variados. Exemplos:
- Processos empresariais desatualizados e pouco eficientes
- Falta de inovação na criação de produtos ou serviços
- Baixa experiência do cliente e dificuldades na interação
- Dificuldade na adaptação a novas tecnologias e tendências
- Estruturas organizacionais rígidas e resistência à mudança